What You Need to Know About…Drum Shells
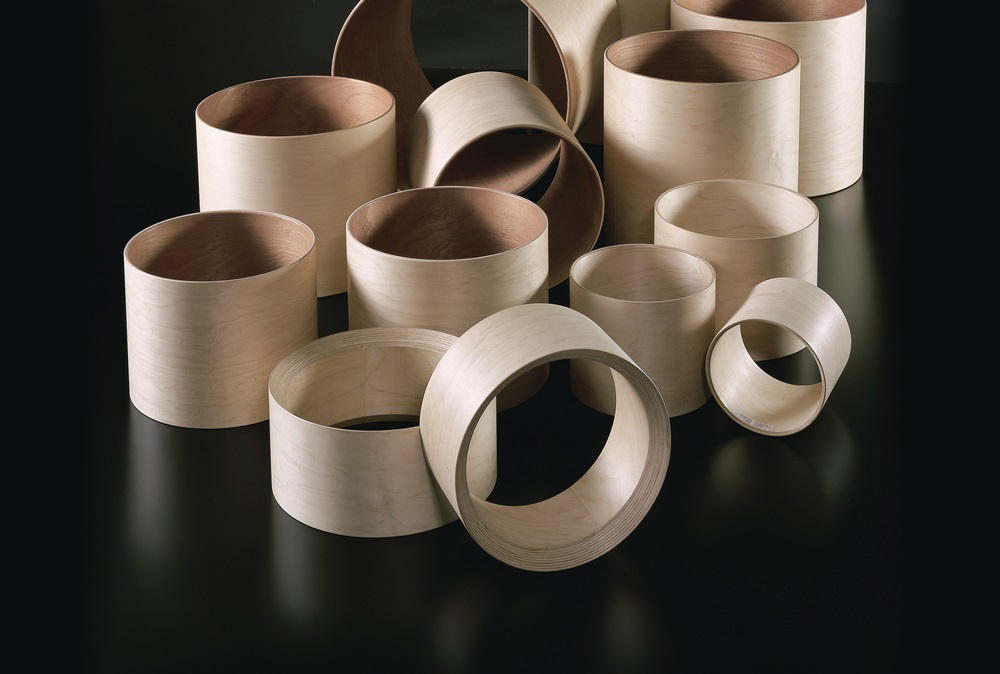
This article originally ran in the Sept/Oct 2011 issue of Drum Business.
by Fran Azzarto
So far in this column, we’ve discussed drumsticks and counterhoops. Now it’s time to dig in and take a look at what we consider to be the heart and soul of every drum—the shell. The shell is the main part of any drum and is really where the sound starts once you hit the head. Whether it’s a wood shell that’s been glued in plies or a metal shell cast in a mold, everything that goes into making a shell has an effect on the sound the drum produces. To answer some questions concerning shells, DB reached out to two specialists in the boutique drum business, Matty Longo of Longo Custom Drums and Curt Waltrip of Joyful Noise Drum Company.
Before we get to specific commentary from Longo and Waltrip, let’s first take a look at the many different materials used to make a shell and the tones that are associated with each. Below is a list of the most common (and some not-so-common) woods, metals, and synthetics used to manufacture drum shells, along with their basic sonic properties.
Wood Types
Maple: Even amount of highs and mids, slightly warm lows. All-purpose.
Birch: Boosted high frequencies, slightly reduced midrange, good low-end punch. Loud and cutting.
Mahogany: Muted highs, smooth midrange, warm/rich low end. Vibrant and resonant.
Walnut: Equal amount of highs, mids, and lows. Big and warm.
Oak: Soft highs, good amount of midrange, slightly warm lows. All-purpose with fairly quick decay.
Beech: Pronounced highs and mids, good low-end punch. Sensitive and focused.
Cherry: Boosted highs, punchy midrange, average low end. Bright and sensitive.
Bubinga: Even amount of highs and mids, rich low end. Sensitive and punchy.
Poplar: Soft highs and mids, boosted low-end warmth. Smooth and eve.
Ash: Pronounced, warm highs and mids, average low end. Throaty and warm.
Exotic woods have been used to make drums for many years. Matty Longo likes to use purpleheart. “It’s a great all-around wood,” he says. “It’s extremely sensitive, with lots of punchy low/mids and excellent presence and cut. The particular lot we’ve been using is at least twenty-five years old and is air-dried.” Curt Waltrip is using some old-growth wood. “Joyful Noise uses reclaimed, submerged old-growth timbers from the Great Lakes as well as wood from Central America for our steam-bent snares and drumsets,” he explains. “Some of the reclaimed, submerged hardwoods we use are flamed red and yellow birch, bird’s-eye maple, quilted maple, blistered maple, and Honduran mahogany.” Advertisement
The bottom line with wood shells is that with more than 3,300 species of timber out in the wild, the potential for new sounds is almost limitless. Each type of wood produces its own unique sound when molded into a cylinder and made into a drum shell, so it’s best to consider which style of music you play and which type of sound will be the best match. Then zero in on a few specific wood types using the basic characteristics outlined above.
Metals
Steel (carbon): Clear highs, average midrange and low end. All-purpose.
Brass: Open highs, mids, and lows. Musically warm and vibrant.
Aluminum: Crisp highs, warm/open midrange and low end. Colorful and sensitive.
Copper: Muted highs, pronounced midrange and low end. Loud and powerful.
Bronze: Muted highs, powerful midrange and low end. Warm and responsive.
Titanium: Clear highs and mids, boxy low end. Clear and focused.
As with wood types, a seemingly limitless number of metal alloys are available to drum manufacturers. So again, consider your musical and playing style, and use the basic sonic properties of the more common metals to help you decide which alloy would be the best match.
Synthetics
Carbon fiber: Even amount of highs and mids, slightly warm low end. Controlled and dry.
Acrylic: Warm highs, mids, and low end. Powerful attack and presence.
Fiberglass: Even amount of highs, mids, and lows. Controlled and focused.
Synthetics have been used for drum shells for around thirty years, but they haven’t been explored as much as metals and woods. Drums made from synthetic materials generally produce more clean and focused sounds than their wood or metal counterparts, and some are surprisingly versatile. Don’t overlook them as you’re finding your sounds of choice. Advertisement
Hybrid Shells
A shell that combines wood and acrylic or metal and wood is known in the current market as a hybrid shell. These combinations of materials will produce distinctive sounds, but are they really usable for drum shells? “Just because you combine two unique sonic qualities in materials, that doesn’t mean they will add up well,” Waltrip says. Indeed, some combinations work better than others, and how the hybrid shell is constructed plays a crucial role in the outcome. As Longo explains, “Doing a hybrid ply or stave shell makes a lot of sense because the wood will run the entire length of the drum’s depth. Therefore it’ll have good energy transfer. But when you put a seam in the shell, it’ll impede the shell’s ability to transfer energy.”
The lesson here is that a blind combination of different materials doesn’t necessarily mean the resultant sound will make musical sense. Be mindful of the types of hybrid shells you choose. Make sure the overall tone is true, clear, and musically viable.
Shell Construction
Drum shells are made in many different ways. Let’s use the same outline as we did in the materials section to see how shell construction affects the sound a drum will produce.
WOOD
Plywood: Long sustain with plenty of volume and varying fundamental pitch
Stave: Short sustain and higher fundamental pitch
Steam-bent: Vibrant with long sustain and true fundamental pitch
Solid: Long sustain and higher fundamental pitch
Segment: Short sustain and higher and more focused fundamental pitch
METAL
Cast: Long sustain and higher fundamental pitch
Spun: Vibrant with long sustain and true fundamental pitch
In addition to the ways different materials and construction options affect the sound a drum shell can produce, the thickness of the shell also has bearing on a drum’s overall tone. According to Longo, “The thinner the shell, the lower the fundamental tone. The thicker the shell, the higher the fundamental tone.” Advertisement
And then there are reinforcement hoops, which many wood models have on the top and bottom of the shell interior. The main purpose of reinforcement hoops is to add strength and stability to the wood, helping thinner shells maintain their true roundness. As drum shell manufacturing has become more technologically advanced, though, the need for reinforcement hoops has less practical use and is employed mostly for tonal effect. “Reinforcement hoops are critical in the tonal character of a drum,” Waltrip says. “The thicker the reinforcement hoop, the more focused or controlled the shell resonance.”
As you can see, there are practically infinite tonal possibilities when you think about all the factors that go into making a drum shell. And that’s before you consider hoop types, drumhead models, snare wire options, bearing edge shapes, and tunings. But using what you’ve learned here—plus what we covered in our counterhoop discussion in the previous issue—you’ll be much better informed when narrowing down the options for the type of drum that will best suit your needs.
And be sure to check out our other What You Need to Know About features here.